
A tour de force, the Morning Glory Vase is largely considered one of Tiffany studios’ greatest achievements. To gain an understanding of why—it is important to understand the events that led to its creation. Tiffany’s lead chemist, Leslie H. Nash claimed that “morning glory glass had its original formula from my green luster glass.” A statement largely contradicted by his own timeline. The first Morning Glory Vases were exhibited at the 1900 Paris Exposition Universelle, fifteen years before Nash purports that he invented Green Luster Glass. Therefore, Nash likely meant that morning glory glass was derived from luster glass in a general sense.
Morning Glories in the Macklowe Gallery Archive
In the 1870s, Leslie's father Arthur worked for Colonel Edward Webb at Whitehouse Glass Works. After years of experimentation, Nash Sr. showed his boss this silver luster glass. The Colonel was disgusted, exclaiming “if you want a tin can go and buy one.” Nash spent the next decades refining the technique to its current iteration— true iridescent glass, both scintillating and lightweight in finish. Nash concludes this anecdote with his usual complaint that Tiffany assumed all the credit for his invention. Nevertheless, it is salient to remember the role of Tiffany’s vision in Nash’s narrative. It was Tiffany who appreciated luster glass, not Webb. And while a man such as Webb could hardly see the potential in Nash’s glass, Tiffany saw the value in its originality—bringing the glass to fruition in spectacular fashion.
Leslie H. Nash, Untitled Leather Notebook, Page 1, Rakow Research Library, Corning Museum of Glass
We begin our journey in the mixing room of Tiffany Studios. The glass world in Tiffany’s time was rife with corporate espionage. Nash was so secretive about his recipes that he mandated that all chemical mixing was to be done alone with the door locked. Chemicals were never referred to or labeled by name, only by number. The key to this chemical code was held by the Nashes. Even spilling of chemicals on the floor was forbidden, as trace remnants could reveal secrets to these unwanted visitors.
The base ingredients of glass were kept in wooden batch boxes. These stackable wooden boxes included the following ingredients:
- Best sand 200 lbs
- Boracic Acid 80 lbs
- Red Lead 170 lbs
- Potash Nitrate 475 lbs
The glassworker would mix the specific chemicals requisite for morning glory luster glass in a wooden bowl. Once mixed, the chemicals were added to the batch box. The chemicals include the following:
- Potash Bichromate 12 ounces
- Iron Oxide (Crocus) 1 pound 8 ounces
- Copper (Black Oxide) 12 ounces
- Silver Nitrate (18 ounces)
- Uranium (Yellow Oxide) (2 ounces)
- Manganese (Needle Crystal) (2 ounces)
- Arsenic (2 ounces)
- Potash Nitrate (6 ounces)
The formula for morning glory glass differed from luster glass, namely due to the 75% increase in silver nitrate (6 ounces to 18 ounces). Nash was the first to include the compound in glass, baffling the entire glass industry with his results. Morning Glory Glass, opposed to other paperweight glass, was reliant entirely on temperature-based chemical reactions. Up until the glass was reheated to 2350 degrees Fahrenheit, the glass remained entirely clear.
Subsequently, the batch box contents were taken outside to the furnace. For demonstration, I will be picturing Tiffany’s sixteen pot furnace.
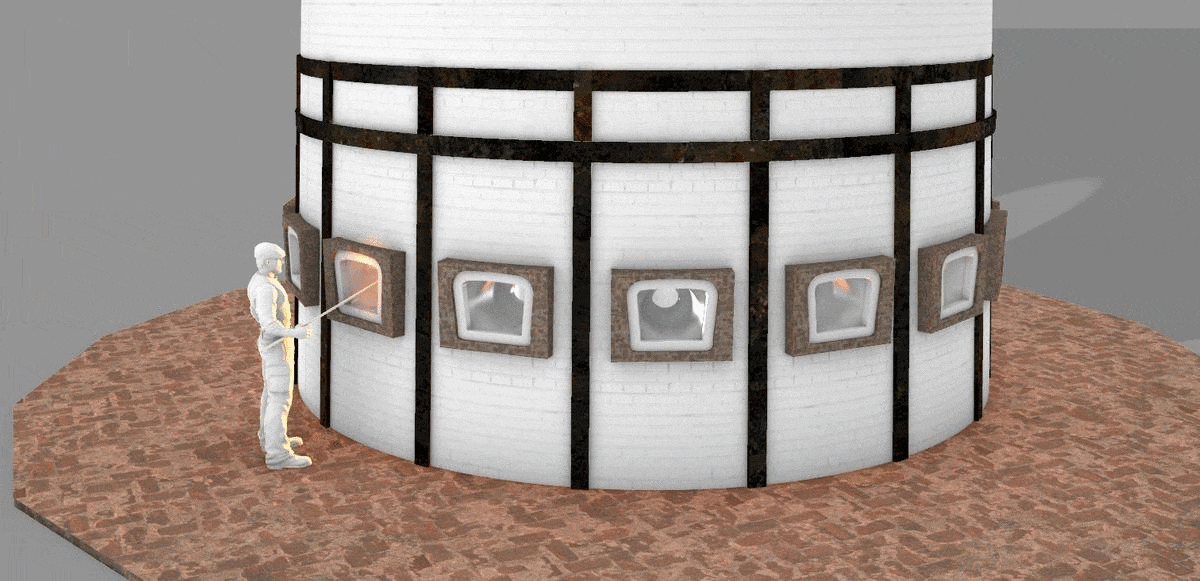




A bubble was blown in and the gather becomes a parison, or partially inflated piece of glass.
The blowpipe was rotated by the glassblower to elongate the parison using centripetal force
The glass was then brought to the glory hole, an apparati used to reheat glass. The glory holes at Tiffany Studios were generally 14” in diameter but could be resized to 8” and 6” using size rings. The blowpipe was held in place by iron stands called pigs. Their grooves would allow lateral movement for the glassblower. The trestle stool allowed the pig to be adjusted for medial movement. The shut iron (corrugated iron flaps) allowed the glory hole to be closed when coming to temperature. Fumes were sucked up by a canopy hood and carried away by the control vent.
Although Tiffany Studios used both gas and oil burners, oil burners were much preferred. Nash included small oil, air, and water tanks in his glory hole diagrams, yet extant photography suggests extensive piping throughout sourced from the building’s central oil, air, and water tanks/lines. For the purpose of this diagram, I have illustrated Nash’s rendition. Oil, air and water were mixed in two inch mixing chambers with the pressure, controlled by needle valves.
Internally, fire bricks called baffles were built up in corners to direct fire where necessary. A skilled glassblower would be able to know where and how to direct the flame to get the desired result. (Please note that although I will be showing the above diagrams once, reheating glass in a glory hole occurs every other step in the rest of the shaping process)

The parison was brought back to the furnace and cased in flint (clear glass). Casing was the application of a layer of glass over a layer of contrasting color.



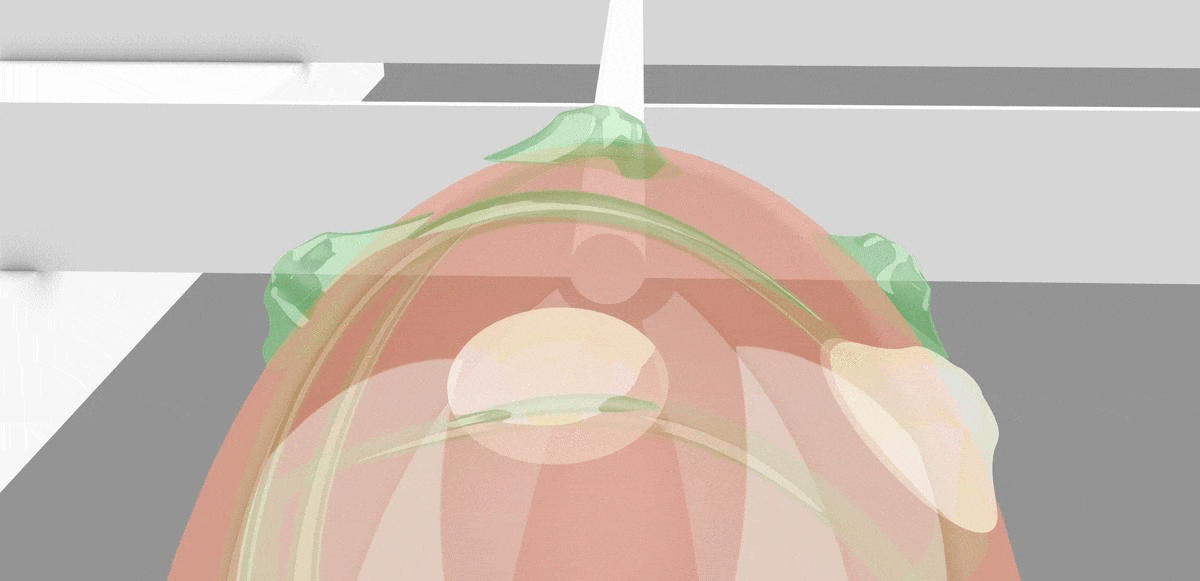

A constriction was made with a pucella near the tip of the gather. Pucella, more commonly known as jacks, consist of two metal blades joined by a spring-like handle. I will refer to these tools as the disambiguation pucella since Nash uses this term in his descriptions. The blades of the pucella were used to touch the sides and flatten the base. All the while the glass blower inflates the vase.
A punty tipped with hot glass was attached to the base, and while a pair of pucella grab the neck, swift taps break the vase at the constriction.
A pair of pucella were used to gently increase the size of the mouth.
A metal tube attached to a conical nozzle called a soffieta was used to further inflate the uppermost part of the vessel.
The handle of the pucella was used to complete the final shaping.
